Navy SAAPER Fall Quarter: Direction Finding
- Jerry Wang
- Dec 31, 2021
- 3 min read
Kickin' Off
My senior year Capstone project is year long, and I will be working with 8 other talented MechE and EE students.
The Navy has come to us for help in their initiative to automate their warships. At port Hueneme, they have a ship that currently serves as a test bed for ship defense systems. Essentially, the Navy would be firing at that ship in order to test their latest ship defense systems, so it’s a good idea to not have people aboard that ship. We were tasked to design a mobile robot that is capable of traversing the complex interior of a navy warship, and it would also be able to manipulate any control dials and switches that would be present in a ship.
However, due to budget and time constraints, we would not be building a full scale robot. Instead we would be building a robot for navigating a 1/3 scale mock ship interior. This is also held as a competition between schools, with the school earning the highest points in the competition being the winner.
The field we were tasked to compete on looks like below:

There are various obstacles, including 60 degree steep ladders, door that need a lever lifted to be opened, high thresholds, narrow corridors, and an instrument panel that requires a knob be turned.
As soon as we received the field descriptions and the CAD for them, both MechEs and EEs got to brainstorming designs for the robot.
Prototyping
Most of the designs we conceived are all mostly geared towards being able to climb the ladders, as we perceive it to be the most difficult obstacle. Narrow corridors can be cleared by limiting the robot’s footprint, the threshold can probably be easily cleared by a robot that is capable of ascending and descending the ladder, and all the lever lifting, door opening, knob twisting can be taken care of by a multi degrees of freedom (DoF) actuator arm.
Here are some inspirations we found that are relevant to the robot design:
Specialized climbing wheels: https://www.youtube.com/watch?v=wWNaqWeH-kg
Actuating treads:
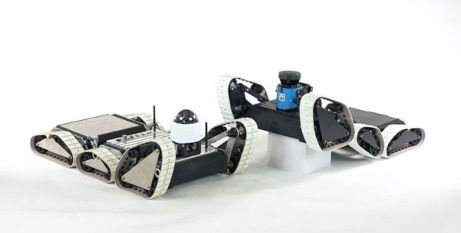
Ladder climber: https://www.youtube.com/watch?v=p5YXVhsy0gw
Telescoping wheels:
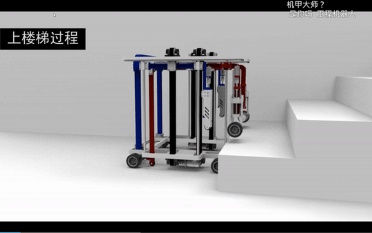
Even though there’s plenty of ideas out there that tackle stair climbing problems, almost none of them are designed to climb stairs steeper than 45 degrees (except the ladder climber), yet our challenge demands 60 degrees, so we also came up with some other creative ideas:
Something that rides on the hand rails on the sides, instead of using the actual stairs
Magnetic treads
Jumping/pole vaulting robot
Legged walking robot
Hook with rope that gets shot up the ladder, catches on something, then a winch pulls the robot up.
After some narrowing down due to limitations of the field, time constraint, and managing expectations, the team is then split into 3 teams to construct prototypes of the remaining 3 ideas: Ladder climber, Wheels on Arms Concept (WoAC), and telescoping wheels.
My Idea
WoAC was my concept, which was inspired by this video: https://www.youtube.com/watch?v=MN-85_Nx7pg where the mobility of a Lego vehicle was greatly enhanced with wheels on pivoting arms at the front and back, to the point where it’s able to even scale vertical obstacles. Since I’m the one responsible for it, I began constructing a motorized critical function prototype out of Lego, to test the feasibility of the concept on our obstacles.
I had some CDs around, so I constructed the “ladder” by stacking them. A bluetooth speaker I had acted as a good substitute for the thresholds.
However, I found the wheel to have reached their limit when the arms are fully extended, thus they are unable to contact the ladder, the robot gets stuck.
Success with Second Iteration
To remedy the last prototype’s pitfall, I constructed another prototype that have treads instead of wheels:
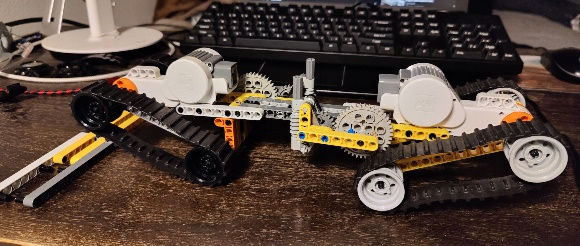
This was a lot more effective then the wheeled prototype, as it doesn’t lose contact with the ladder.
Very fortunately, we had a collaboration with ASME, who constructed a set of field obstacles (ladder, door) exactly identical to the CAD provided to us by the Navy. This is a great aid to helps us validate designs and iterate rapidly.
I tested my dual tread prototype, and it was able to climb the ladder, with me manually adjusting the pivot angle and controlling the two motors.
Other prototypes were constructed as well, but after some discussion with the team over the pros and cons of each design, we determined that treads are the most reliable design because they are proven to be effective in most obstacle clearance tasks, but they are also the simplest to implement, with less actuating parts compared to other concepts. Also because of the ease of the tread prototype climbed the obstacle, we chose the treads as the direction to pursue the development of the robot.
And that is a wrap for the fall quarter. We were happy to have a robot design direction that has been validated by prototyping and we were looking forward to actually constructing the robot, along with development for the actuator and electrical systems for the rest of the robot.
Comments